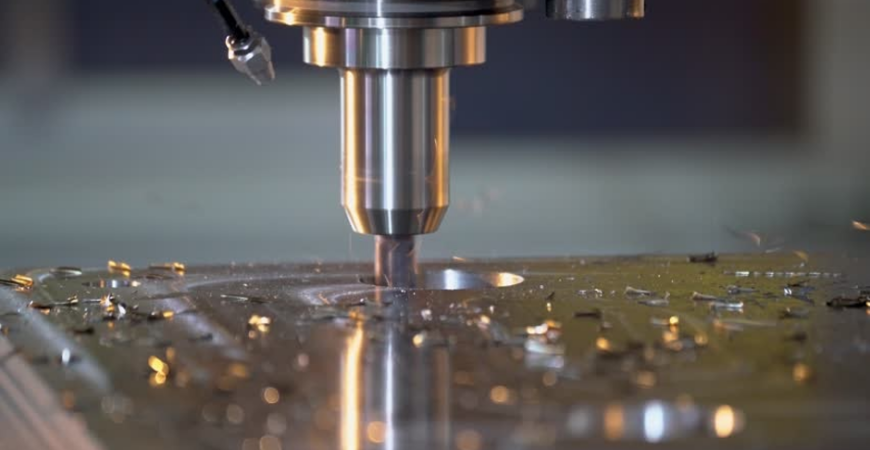
What is CNC Milling?
What does CNC stand for?
A computer numerical control (CNC) mill allows the machine to be moved and monitored by computer control. The benefits of using a CNC mill allows for a more accurate and timely manufacturing. Milling is the cutting and drilling process of materials.
This includes materials such as:
- titanium
- alloy steels
- engineering plastics
- aluminium alloys
- stainless steel
- duplex and super duplex
- brass
- bronze
- copper
How does a CNC machine work?
A milling machine uses a rotating cylindrical tool called a milling cutter, regardless of whether it is operated manually or by CNC. It is placed in a spindle and the shape and size of it can vary. The main difference between a milling machine and any other drilling machine is the ability to cut and travel around different axes at different angles.
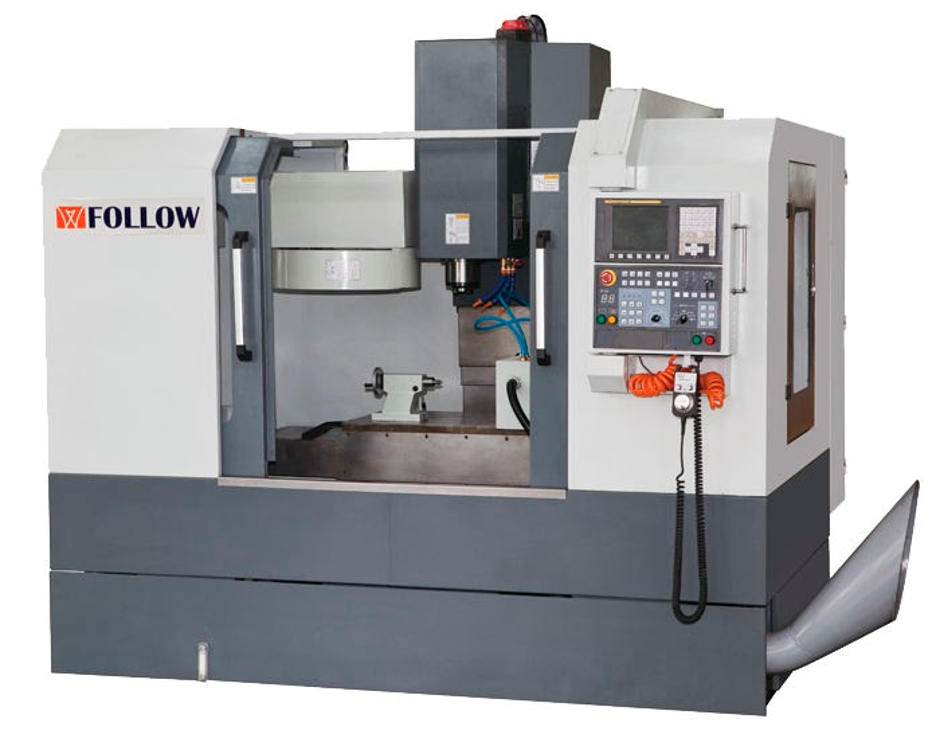
The CNC machining process
It all starts with designing a computer-aided design (CAD) model. A commonly used program for CAD is Autodesk® Fusion 360™. Using this, you can effectively sketch and model 3D parts.
The next step is converting the CAD model into a CNC program. This is done through computer-aided manufacturing (CAM) software. Software such as BobCAD-CAM, CAMBAM, CAMWorks, Fusion 360 and many more use a numerical control (NC) to create detailed instructions (G-code) that drive CNC machines.
We then set up the CNC milling machine. This is done by fixing the workpiece to the worktable of the machine using a holding device such as a vice, along with attaching the milling tools to the machine spindle. Depending on the complexity of the design, other tools may be required.
Lastly, the milling operation is executed. Just like above, depending on the complexity of the design it will go through a variety of processes. At first, the CNC machine will cut small pieces to form an approximate shape and form of the final design and then proceed to go into further accuracy and precision to get the exact features and specifications of the final design.
This all can be broken down into 3 steps:
- CAD (computer-aided design)
Input: Sketch by human
Result: A design
Output: A file that can be read by a CAM program
- CAM (computer-aided manufacturing)
Input: a file from a CAD program, or manual instructions from a human
Result: a set of instructions for a CNC machine
Output: a file which can be read by a CNC machine
- CNC (computer numerical control)
Input: A file from a CAM program, or manual instructions from a human
Result: Signals for stepper motors or servos
Output: Machined workpiece
What are the advantages of CNC?
- Accuracy of the final product
- Efficiency and time
- Safety of the user
- Uniformity in design
- Low maintenance
- Reliability
- No room for human error
- Lesser number of operations required
- Could run 24 hours a day
- Flexible scalability
Disadvantages of CNC machines
- The first production run will likely be more expensive than the latter ones
- A skilled operator is required
61 comments
Comments are closed.
November 14, 2024
Good day! Do you know if they make any plugins to
assist with Search Engine Optimization? I’m trying to get
my blog to rank for some targeted keywords but I’m not seeing very good
results. If you know of any please share. Kudos! You can read similar article here:
Eco blankets
November 15, 2024
ggolxl
January 1, 2025
I think this website holds very great pent subject material posts.
https://www.droversointeru.com
January 25, 2025
4s7mho
January 30, 2025
You could definitely see your expertise in the work you write. The world hopes for even more passionate writers like you who aren’t afraid to say how they believe. Always follow your heart.
https://www.zoritolerimol.com
February 9, 2025
UID_74743238###
Ini dia! 🎉🎉 ASN BKN Ubah Pola Kerja yang baru dan efisien! 🎉🎉.
February 9, 2025
UID_83344528###
Inilah 🎉🎉 Pupuk Inovatif Kebun Riset Kujang yang bikin Wamen BUMN bangga! 💪🏻🇮🇩
February 9, 2025
UID_21891068###
Takjub 😮 dengan fenomena serbu gas? Yuk, baca Warung Tatang Diserbu Warga dan temukan faktanya! 🕵️♀️👀
February 10, 2025
UID_25978847###
situs terbaik hanya di slot gacor agentotoplay
February 10, 2025
UID_95859078###
Baru-baru ini, para pemain Mahjong Wins 3 dikejutkan dengan bocoran RTP yang diklaim bisa meningkatkan peluang kemenangan secara signifikan. Banyak yang percaya bahwa informasi ini membantu mereka mendapatkan hasil yang lebih konsisten dalam permainan. Jika Anda ingin tahu lebih lanjut, cek bocoran RTP Mahjong Wins 3 hari ini dan lihat apakah strategi ini benar-benar efektif.
February 11, 2025
UID_57331425###
Skandal terbaru mengguncang komunitas pecinta game slot setelah seorang admin terkenal, Rachel, dikabarkan tertangkap membocorkan pola kemenangan Gate of Olympus. Banyak yang bertanya-tanya apakah informasi ini benar-benar akurat atau hanya sekadar rumor yang beredar di kalangan pemain. Simak lebih lanjut detailnya dalam artikel admin Rachel tertangkap bocorkan pola Gate of Olympus.
February 11, 2025
UID_17136916###
Kisah inspiratif datang dari seorang tukang ojek online asal Tangerang yang berhasil membawa pulang hadiah fantastis setelah bermain Mahjong Ways 2. Dengan modal kecil, ia sukses mengubah nasibnya dan meraih kemenangan besar senilai 200 juta rupiah. Penasaran bagaimana caranya? Simak kisah lengkapnya di artikel tukang ojek online menang 200 juta dari Mahjong Ways 2.
February 12, 2025
UID_87427935###
Cek yuk! 🚍👮♂️Operasi Keselamatan 2025 Polres Ciamis Siapa tahu bus favoritmu jadi sasaran! 😱👍
February 13, 2025
UID_18563832###
Ini yang di ganti >>> Yuk, ketahui lebih lanjut tentang Syarat Gabung OECD dan Pentingnya Ratifikasi Konvensi Antisuap di sini! 🕵️♀️🔎📚.
February 13, 2025
UID_83003169###
Kenalan yuk! 🤝 Dengan guru inspiratif ini, Guru Dede Sulaeman yang mengajarkan cara merapikan pakaian di kelasnya. 👕👚🎓
February 13, 2025
UID_97211224###
Yuk, sehat bersama! 👨⚕️👩⚕️ Cek kondisi tubuh kamu di Program Cek Kesehatan Gratis sekarang juga! 💉🌡️ Selalu jaga kesehatan, ya! 🏥💖
February 14, 2025
UID_55590637###
situs terbaik hanya di slot gacor agentotoplay
February 15, 2025
Thank you for your sharing. I am worried that I lack creative ideas. It is your article that makes me full of hope. Thank you. But, I have a question, can you help me?
February 15, 2025
Your article helped me a lot, is there any more related content? Thanks!
February 17, 2025
Can you be more specific about the content of your article? After reading it, I still have some doubts. Hope you can help me.
February 21, 2025
Can you be more specific about the content of your article? After reading it, I still have some doubts. Hope you can help me.
February 21, 2025
V46eYkH17qC
February 21, 2025
QIWNX2G55YR
February 21, 2025
ZUHnIXkhrCL
February 21, 2025
azXPFZYcqMa
February 21, 2025
8qQ000d5BHZ
February 21, 2025
wIsEzTsxerT
February 21, 2025
ea9zTcX6xUW
February 21, 2025
LTtCTKbxzJB
February 21, 2025
Iz8pJ9J4UVn
February 21, 2025
G8UNyoBvPTR
February 21, 2025
YQZqGycwU3O
February 21, 2025
nlTHorlkWOf
February 21, 2025
7ywCKH86AEt
February 21, 2025
znHHZ6znlYt
February 21, 2025
aPOygiEYYxA
February 21, 2025
RSMrKAhSfbr
February 21, 2025
XbFB1KdNhSv
February 21, 2025
JGMB0bfhiZP
February 21, 2025
u83kPvmYviv
February 21, 2025
PKmdH94bTEc
February 21, 2025
6gs4L0PI4by
February 21, 2025
WKZLRwA55aM
February 21, 2025
wZvlOiV1A6H
February 21, 2025
SirgTYN7Kmb
February 21, 2025
4TmHO8iH4hR
February 21, 2025
ZKdSzDMQ6bL
February 21, 2025
mrObnaSoMUz
February 21, 2025
VWvUUCw9oIC
February 21, 2025
zCvZttjZxe5
February 21, 2025
ybGMJu3QoyD
February 21, 2025
kANQ8XTUVGL
February 21, 2025
jmmsKNKtgXo
February 21, 2025
5vQu8De1P5d
February 21, 2025
gcBepef6ghW
February 21, 2025
BxDzsIhOoDB
February 23, 2025
Your article helped me a lot, is there any more related content? Thanks!
February 23, 2025
Your point of view caught my eye and was very interesting. Thanks. I have a question for you.
February 25, 2025
Your article helped me a lot, is there any more related content? Thanks!
February 26, 2025
Your article helped me a lot, is there any more related content? Thanks!
March 5, 2025
Thanks for sharing. I read many of your blog posts, cool, your blog is very good. https://accounts.binance.com/da-DK/register-person?ref=V2H9AFPY